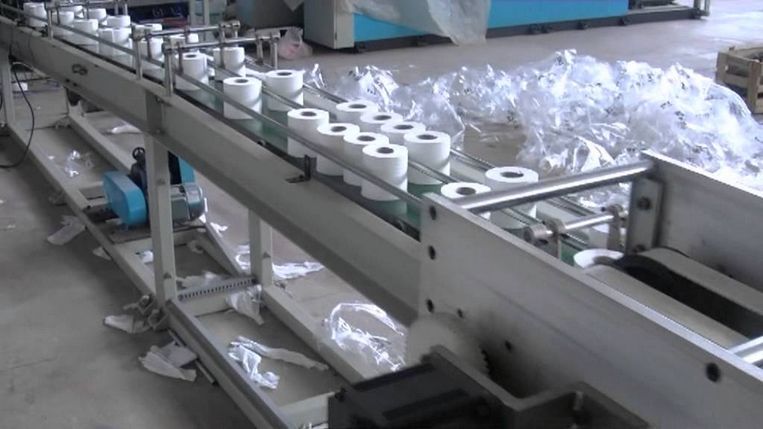
Accounting for manufacturing businesses: 6 key stages in the implementation process
What Is A Manufacturing Account?
A manufacturing account is an account in the general ledger of a businesses which summarizes the manufacturing costs of finished goods during an accounting period.
Such accounts are prepared by the manufacturing concerns for the purpose of finding out the cost of production of the goods manufactured and the profit that has been made by manufacturing department.
For a manufacturing business the manufacturing account needs to be prepared before completing the trading, profit and loss accounts.
The major objective of preparing a Manufacturing Account is to determine the specific costs associated with finished goods produced.
The cost of finished goods manufactured can then be entered in the Trading, Profit and Loss Account, otherwise called Income State, as the equivalent of purchases for a purely trading company in order to determine the cost of goods sold and gross profit.
This helps in improving the cost optimization and effectiveness of manufacturing activities.
What Are The Broad Components of Manufacturing Costs?
Manufacturing cost fall into three broad components: materials, labour, and overhead.
Therefore to calculate total manufacturing cost, you sum up the three different cost components: costs of direct materials, direct labour and manufacturing overheads. Expressed as a formula, that’s: Total manufacturing cost = Direct materials + Direct labour + Manufacturing overheads.
The difference between Trading Account and Manufacturing Account is, the trading account gives the Gross profit made by the company whereas the Manufacturing account derives the cost of finished goods produced by the company.
Stages In Accounting Implementation For Manufacturing Business
Accounting for a manufacturing business deals with inventory valuation and the cost of goods sold. These concepts or stages are uncommon in other types of entities, or are handled at a more simplified level.
A manufacturing business must use a certain amount of raw materials, work-in-process, and finished goods as part of its production processes, and any ending balances must be properly valued for recognition on the company balance sheet. This valuation requires the following activities or stages.
1. Direct cost assignment.
Costs are assigned to inventory using either a standard costing, weighted-average cost, First In First Out (FIFO) or Last In First Out (LIFO.)
2. Overhead cost assignment.
Factory overhead costs must be aggregated into cost component and then allocated to the number of units produced during a reporting period, which increases the recorded cost of inventory. The number of cost components should be minimized to reduce the amount of allocation work by the accountant.
3. Impairment testing.
Also known as the lower of cost or market rule, this activity involves ascertaining whether the amount at which inventory items are recorded is higher than their current market values. If so, the inventory must be written down to the market values. This task may be completed at relatively long intervals, such as at the end of each annual reporting period.
4. Cost of goods sold recognition.
At its most basic level, the cost of goods sold is simply beginning inventory, plus purchases, minus ending inventory. Thus, the derivation of the cost of goods sold is really driven by the accuracy of the inventory valuation procedures that were just described. In addition, any abnormal costs incurred, such as excessive scrap, are not recorded in inventory, but instead are charged directly to the cost of goods sold. This calls for a detailed scrap tracking procedure. Also, costs may be assigned to specific jobs (known as job costing) and then charged to the cost of goods sold when the inventory items in those jobs are sold to customers.
5. Derivation of Cost of Raw Materials Consumed
The formula for deriving cost of raw materials consumed for an accounting period for a manufacturing business can be summarised as follows:
Cost of Raw Materials Consumed = Raw material purchases + Beginning raw material inventory – Ending raw material inventory = Cost of Raw materials consumed
6. Derivation of Cost Of Goods Manufactured
Cost of Goods Manufactured = Cost of Raw materials consumed + Direct labor + Direct expenses + Beginning WIP inventory – Ending WIP inventory + Manufacturing Overhead =
Definition of Terms
Direct labor is the gross wage cost of all the labor associated with manufacturing products. The labor included must relate to those employees who are directly working on the products being produced. As with materials it must be possible to easily identify, track or count the labor to a particular unit of production.
Direct expenses are costs other than direct materials or labor which can be directly associated with units of production. An example of a direct cost would be a royalty cost paid on each product.
The adjustment for work in process inventory is necessary as the purpose of the account is to show the manufacturing cost of goods completed during the accounting period regardless of when they started in production.
Manufacturing overhead is all the other costs necessary to run the manufacturing operation but which cannot be directly associated with the product such as indirect labor, indirect materials, and other indirect manufacturing costs.
How To Prepare Manufacturing Account
The main objective of preparing a manufacturing account is to determine the actual cost of goods available for sales otherwise called finished goods.
The account is simply prepared by closing the temporary cost accounts and adjusting the raw materials (RM) and the work in process (WIP) inventory accounts using a closing journal entry. Each cost account is closed and the balances transferred to the manufacturing account.
Work-in-progress (WIP) inventory is a production and supply-chain management term used to describe partially finished goods awaiting completion. WIP inventory is a component of the inventory asset account on the balance sheet. These costs are subsequently transferred to the finished goods account and eventually to the cost of sales now becoming a component of the income statement.
Manufacturing, trading, profit and loss account is maintained by all manufacturing organisations to help in the formation of final accounts of such businesses.
Manufacturing overhead account is calculated by the addition of indirect factory expenses like machine repairs, depreciation, insurance, factory supply, electricity, etc. Non-manufacturing entities or what is called trading entities are generally involved in the purchase and also sales of goods at a profit.
Features of A Manufacturing account
All the expenses relating to manufacturing goods are debited.
It shows only the figures of materials consumed instead of showing the figure of opening stock, purchase and closing stock separately.
Opening stock of Work in Progress (WIP) is debited and closing stock of WIP is credited to manufacturing account.
The amount received from the sale of scrap is credited to manufacturing account.
The balance in the manufacturing account is the cost of production or manufacturing profit depending on the type of manufacturing account prepared.
Importance of manufacturing account
It ascertains the cost of goods manufactured.
It shows the profit or loss earned by a manufacturing department.
It provides a basis for fixing the price of a product.
It helps the management to evaluate the performance of the manufacturing department.
It helps to control manufacturing cost.
FAQ (Frequently Asked Questions)
1. What are the Features of Manufacturing Account?
Ans) Some of the important features of manufacturing account are:
All the expenses are debited that are related to manufacturing goods.
The figure of opening stock, purchase and closing stock is not shown separately. Instead, it only shows the figures of materials consumed.
The opening stock of work in progress is debited to manufacturing account while the closing stock of work in progress is credited.
The sale of scrap amount gets credited to manufacturing account.
Depending on the manufacturing account prepared, the manufacturing account balance is either the cost of production or the manufacturing profit.
2. What is the Difference Between a Trading Account and Manufacturing Account?
Ans) The financial statement which considers all the elements of cost, income and expenditure is known to be the trading account. It determines the profitability of the company. On the other hand, manufacturing account determines the expenses that are incurred for manufacturing a product.
In a financial year, the trading account gives the verdict of profit or loss in a company while manufacturing account denotes the cost of the product manufactured.
The information of manufacturing account gets featured in trading account while manufacturing account consists of the expenditure caused by the product manufactured.
A trading account helps in the creation of the final balance sheet of a company. Manufacturing account details the requirement for creating a trading account.
Direct revenue and expenses are displayed in the trading account. Operating expenditure for product manufacturing gets displayed in manufacturing account.
You can reach us on telephone/whatsapp message on 08033857245 or 0803 239 3958. You can also send us an email info@skytrendconsulting.com
Need an accounting software solution for your business? Whatsapp us on 0803 239 3958. You have an article or review on financial implementation or an accounting solution you want us to publish, send to blog@skytrendconsulting.com.
READ ALSO! Accounting software implementation: 5 key stages in a new accounting system
READ ALSO! Skytrend Consulting: Financial services and accounting solutions company
READ ALSO! SAGE 50 ACCOUNTING SOFTWARE: 8 KEY BENEFITS FOR YOUR BUSINESS
READ ALSO! SAGE 50 PEACHTREE ACCOUNTING SOFTWARE – ALL YOU NEED TO KNOW
READ ALSO! BBNaija Dorathy Launches Lingerie Line, Says Priority Is Making Busty Women Look Good
READ ALSO! How To Empower Yourself And Generate Income From Mutual Funds
READ ALSO! Why The North Remains Headquarters Of Poverty In Nigeria — Kingsley Moghalu